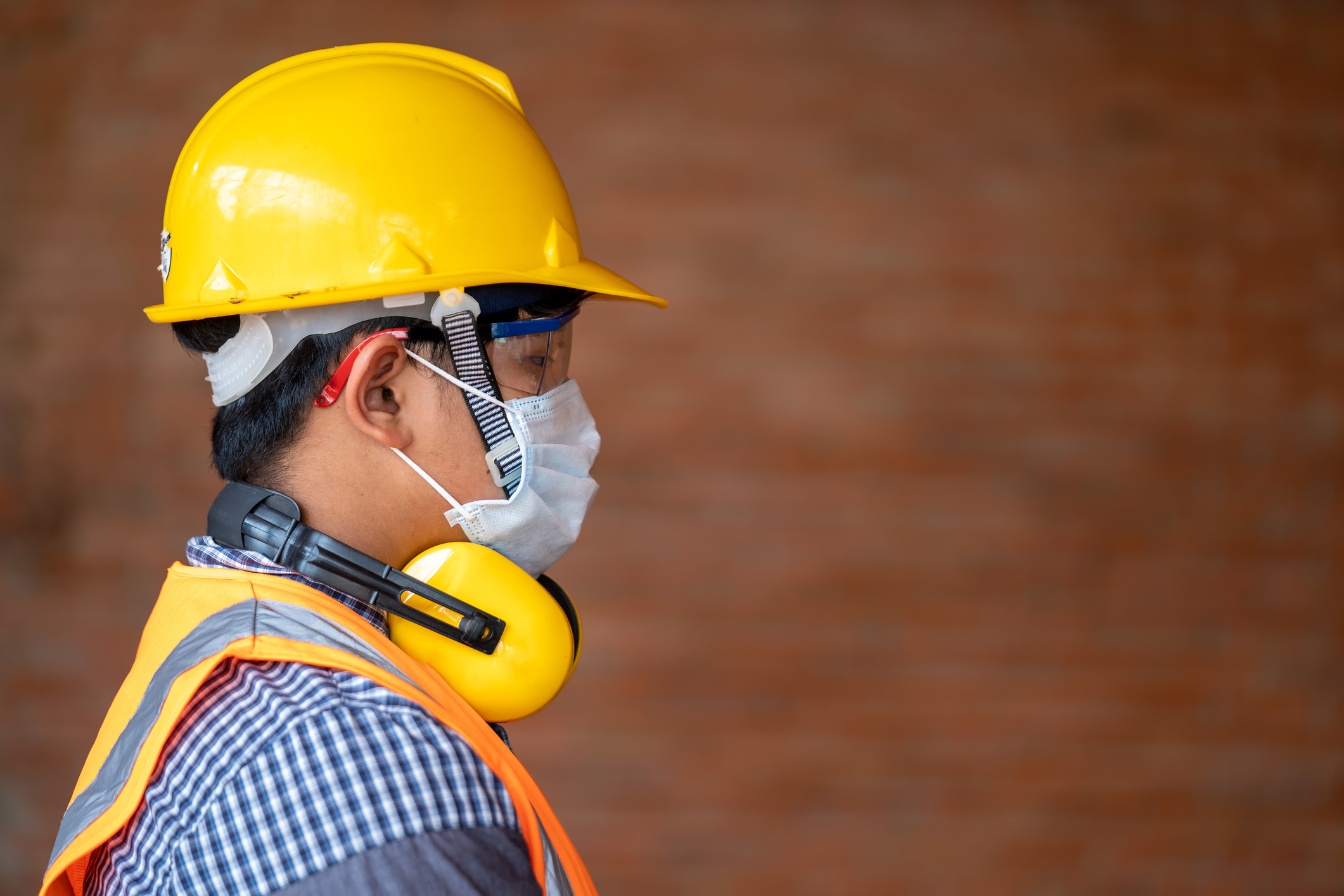
With productivity in the construction industry historically flatlining, surely the pandemic can help us reset and reinvent solutions to the productivity challenge? By Paul Beeston
Construction industry productivity had flatlined prior to the covid-19 pandemic, with our sector showing less improvement than other sectors of the economy. Organisation for Economic Co-operation and Development (OECD) data shows the UK Index of Production in Construction showing only modest improvement since the 1990s. It took a global pandemic for project teams to take an active and daily interest in site productivity as practical completion dates loomed and as yet un-contracted projects grappled with coronavirus costs and risks.
Extra costs
Covid-related productivity challenges have manifested themselves as costs and for many contractors that may be their own costs for live projects. For projects moving through procurement stages post March 2020, estimators up and down the supply chain will have been balancing inflationary productivity challenges and deflationary market conditions.
Inflationary cost impacts may be felt in additional preliminaries, including welfare, cleaning and other compliance measures with site operating procedures (SOPs) along with any prolongation impacts. For physical work content, the amount of output that can be achieved for a given labour input will have (in all likelihood) decreased as a result of compliance with SOPs. Finally, a client’s allocation of risk in contract conditions may have caused estimators to consider, and possibly add cost.
Different trades, and when assembled into projects, different construction typologies in different sectors have different densities of labour (the manhours per pound of construction spend). Warehouses and infrastructure typically have lower density and residential, repair and maintenance have higher labour density. Not only is the impact of covid evolving, its impact is inconsistent.
‘One size does not fit all’
Although productivity has flatlined, there is no shortage of strategies, plans and fixes parachuted into our industry. Often with a pick and mix series of thoughts; sometimes with a strong central idea like Latham’s partnering, Egan’s lean construction and Farmer’s MMC, among others. Some ideas have stuck, forcing their way into legislation, others have been adopted widely as good practice, but regardless none have pushed productivity to come on leaps and bounds.
Construction is not a ‘one size fits all’ industry. Bold thinking and big ideas are useful in nudging the industry on, however, most projects are shaped by thousands of interactions between disciplines and conflicting demands. The opportunities for wholesale adoption of the latest industry panacea are few and far between. Does that make project teams luddites or pragmatists?
Reset and reinvent
Productivity is one of the Construction Leadership Council’s (CLC) ‘reset’ strands of its Covid-19 Roadmap for Recovery. However, given the historical flatlining, it must surely also be carried through into the ‘reinvent’ phase. So, what may work to reset productivity and reinvent solutions to the productivity challenge?
First, understand what impacts productivity. In July, the CLC published a toolkit to assess the cost of covid-19 productivity. It included a series of metrics for measuring productivity, which can be used to forecast, benchmark between projects, examine what works. Engrain in teams the mantra that productivity impacts construction costs.
Second, take time to consider how to build what is being designed – early and often. The principles of MMC and DfMA should be thought about, and they are not all about volumetric units (‘Category 1’ in the government definition framework). The full spectrum of MMC should be considered, along with the simpler notion of ‘buildability’. A focus on ‘how’ to build it may change the ‘what’ or the ‘why’.
Thirdly, embrace the creativity of construction. The construction stages of a project (or operational stages) should not be a brake on the quality of design. Throughout the early stages of lockdown construction teams responded quickly and innovatively to keep sites going safely to maintain production. Construction is a creative process and that should be embraced in design stages.
A positive legacy?
The focus on productivity that has accompanied the global pandemic may be a positive legacy. As the industry navigates tough times a more productive industry may enable schemes to deliver more with less.
Finally, the drive for productivity should always be placed in the context of value. Construction industry ‘output’ is more than the square feet of offices, hospital bed spaces or kilometres of road delivered. Improving productivity should enable better outcomes meeting the value aspirations of clients. The legacy of our buildings and infrastructure (from carbon to community wellbeing) lasts for decades.
Paul Beeston is a partner at RLB and part of the working group for the Construction Leadership Council’s productivity toolkit.